В отечественной нефтегазовой индустрии ежегодно наблюдается тенденция активного роста объёмов добываемого попутного нефтяного газа (ПНГ). При этом встает вопрос рационального применения ПНГ, который в свою очередь является одним из наиболее важных показателей, характеризующих уровень промышленного развития любой компании и отрасли в целом. Однако, до недавнего времени существенные объемы ПНГ сжигались на факелах, что, во-первых, наносило огромный ущерб окружающей среде, а с другой – подразумевало снижение эффективности производства сырья. В настоящее время переработка и утилизация попутного газа реализуется по двум основным направлениям: энергетическому, когда ПНГ используют в качестве топлива, и нефтехимическому, позволяющему получать ценные химические продукты с высокой добавленной стоимостью [1-3].
Состав добываемого газа зависит от материнской породы залежи и геологической истории формирования данных. В процессе добычи природного газа скважинная продукция содержит большое количество вредных примесей (сероводород, углекислый газ, механические отложения и т.д.), которые могут вызвать коррозионно-активное разрушение выкидных линий и внутрипромысловых сборных коллекторов. Также в процессе транспортировки в зависимости от режима течения может происходить по мере снижения давления и температуры выделение капельной жидкости водяных паров и конденсата.
Ключевым требованием подготовки является товарное качество согласно ГОСТ 5542-2014 «Газы горючие природные промышленного и коммунально-бытового назначения. Технические условия», регламентирующий требования по числу Воббе (от 41,20 до 54,5 МДж/м3); массовой концентрации механических примесей (не более 0,001 г/м3), сероводорода (не более 0,02 г/м3) меркаптанов (не более 0,036 г/м3); молярной доли кислорода (не более 0,05 %) и диоксида углерода (не более 2,5 %); а также других физических показателей [4].
Промысловая подготовка газа включает в себя следующие процессы: очистка от механических примесей, агрессивных примесей, тяжелых углеводороводов; осушка до необходимой точки росы. Все данные процессы осуществляются на установках комплексной подготовки газа (УКПГ), которая представляет определенный состав технологического оборудования и вспомогательных систем, обеспечивающих сбор и обработку природного газа и газового конденсата. Пример технологической схемы приведен на рис.1.
Способ осушки природного газа выбирается в зависимости от содержащегося количества конденсата и необходимой точки росы по воде, определяемой, как более низкую, чем минимальная температура, которая обеспечивает его безгидратную транспортировку по газопроводу или переработку. Степень осушки должна быть на 3-5 градусов ниже минимально возможной температуры в газопроводе [1].
Среди основных способов осушки газа выделают: абсорбцию; адсорбцию; низкотемпературную сепарацию.
Абсорбция представляет собой селективное поглощение жидкими абсорбентами паров воды. В качестве основных поглотителей используются высококонцентрированные растворы гликолей: метанол, этиленгликоль, диэтиленгликоль, триэтиленгликоль. Два последних отличаются высокой гигроскопичностью и способностью регенерировать без больших потерь из-за низкой летучести. Вследствие низкого давления насыщенных паров гликолей потери их при осушке незначительны и колеблются в пределах от 5 до 35 г на тысячу кубических метров газа.
Абсорберы по способу контакта взаимодействующих фаз делят на три группы: поверхностные, барботажные и распыливающие.
Установка осушки диэтиленгликолем и триэтиленгликолем работает согласно следующему принципу: поступающий с абсорбционной установки газ вначале проходит сепаратор, в котором осаждается капельная влага, затем газ направляется под нижнюю тарелку абсорбера 4. Поднимаясь через тарелки, он контактирует с раствором гликоля, подаваемым на верхнюю тарелку абсорбера. Концентрированный раствор гликоля постепенно насыщается парами воды и опускается в нижнюю часть абсорбера, откуда под собственным давлением через теплообменник 6, выветриватель 8 и фильтр 9 направляется в выпарную колонну (десорбер) 13 для восстановления первоначальных свойств (регенерируется). Выпарная колонна состоит из двух частей: собственно колонны с насыпкой колец Рашига 14, служащих для увеличения поверхности контакта, и печи 15, в которой происходят нагревание раствора гликоля и испарение воды при сжигании таза. В кипятильнике может поддерживаться температура раствора гликоля от 150 до 180° С, а в верхней части выпарной колонны — от 105 до 107° С. Регенерированный (концентрированный) раствор гликоля забирается насосом 16 и через теплообменник 6 и холодильник 7 снова поступает на верхнюю тарелку абсорбера. Осушенный в абсорбере газ, поднимаясь в верхнюю часть колонны, проходит в жалюзийный каплеуловитель 3, в котором удерживаются капли гликоля, и направляется в магистральный газопровод. Раствор гликоля, отделяемый в каплеуловителе, поступает по линии 2 на регенерацию в выпарную колонну. Для снижения потерь гликоля при регенерации в верхней части выпарной колонны установлены холодильник 12, в котором поддерживается температура около 80° С, и сепаратор 11 с каплеотбойной насадкой [5].
Экономичность работы установок рассмотренного типа во многом зависит от потерь гликолей, которые в основном происходят в результате неправильно выбранного температурного режима регенерации и отсутствия каплеулавливающих приспособлений как на абсорбере, так и на сепараторе. Больше всего гликоли теряются в результате образования пены при контакте газа с абсорбентом. Интенсивность пенообразования зависит от чистоты раствора и наличия в осушаемом газе углеводородного конденсата, а также пластовой воды [11].
Практикой установлено, что для успешной осушки газа в системе должно циркулировать не менее 25 л гликоля на 1 кг абсорбируемой воды и следует применять возможно большее число 10-12 тарелок в абсорбере. На рис. 1 представлена схема абсорбционной осушки.
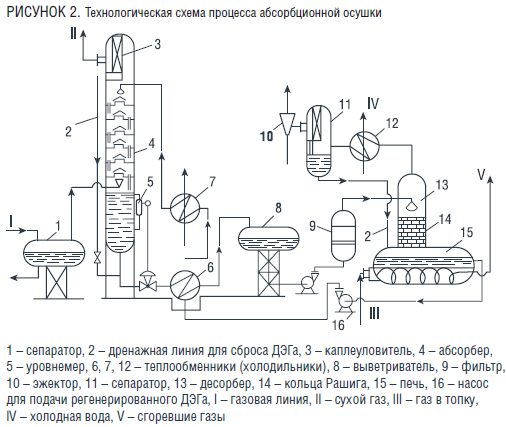
В зависимости от степени регенерации выбирается метод, при 96-98% применяется десорбция при давлении близком к атмосферному, иначе для получения более концентрированного раствора десорбцию проводят под вакуумом, снижают парциальное давление углеводородов подачей отдувочного газа или вводят реагент (толуол, ксилол, бензол), образующий азеотропную смесь [2].
Основными преимуществами абсорберов являются:
· глубокая осушка;
· низкие эксплуатационные расходы;
· простота автоматизации процесса;
· малые перепады давления;
· возможность осушки агрессивного газа, который не применим при использовании твердых сорбентов.
Основными недостатками являются:
· Необходимость повышения температуры газа выше 40° С;
· Возможность вспенивания поглотителей.
Процесс абсорбции целесообразно проводить при пониженной температуре. С ростом давления растворимость газа увеличивается. Поэтому процесс абсорбции целесообразно проводить при повышенном давлении. Обратный процесс – десорбцию – лучше проводить при пониженном давлении.
Установка имеет по два блока абсорбции и десорбции. На первой ступени газ осушается гликолем с концентрацией 96-97 %, а затем поступает в адсорбер второй ступени, где доосушается гликолем с концентрацией 99,5-99,6 %. В десорбере первой и второй ступени влага из насыщенного гликоля десорбируется соответственно при атмосферном давлении и под вакуумом. В ряде случаев для достижения высокой депрессии и низкой температуры точки росы используют комбинированную осушку (рис. 2). На первой ступени осушку производят абсорбционным методом, для удаления капельной влаги и предотвращения забивки пор адсорбентов, используемых в адсорбционной осушке второй ступени. газового потока и обеспечивает низкую точку росы [7].
Абсорбционный метод применяется в системах, где достаточно среднего уровня осушки газа с ТТР до -40 °С. Применяется в основном для осушки природного газа, транспортируемого по магистральным трубопроводам. Глубокую осушку (ТТР ниже - 40 °С) проводят с помощью установок, реализующих адсорбционный метод очистки технологических газов.
Адсорбция используется практически при любых давлениях. Адсорбционная осушка газа основана на поглощении паров воды из природного газа твердыми поглотителями–адсорбентами. Как правило, в качестве адсорберов используются: бокситы (природные минералы, состоящие в основном из Al2O3); активированная окись алюминия (очищенный боксит); силикагели (вещества, состоящие из окиси кремния и получаемые с помощью химических реакций); молекулярные сита (натрийкальциевые силикаты).
Осушка происходит в адсорберах в течении 35 ч. После этого газ направляется в другой адсорбер, а отработавший–на регенерацию–выпаривание влаги нагреванием до 350-400ºС. Регенерация продолжается до 20 ч, в зависимости от температуры газа и его влажности.
На сегодняшний день выделяют следующие основные типы адсорберов: с неподвижным/слоем адсорбента; с движущимся слоем адсорбента; с псевдоожиженным слоем адсорбента.
По способу протекания процесса адсорбция делится на:
1) физическую адсорбцию, за счет действия поверхностных сил и капиллярной конденсации (например, осушка газа от влаги);
2) хемосорбцию, за счет химического взаимодействия адсорбента с поглощаемым веществом.
Среди основных преимуществ адсорбционной осушки можно выделить:
· низкую точку росы осушенного газа (ТР до - 100 °С);
· большую величину разности точки росы влажного и осушенного газа в широком диапазоне параметров исходного газа;
· возможность извлечения из газа вместе с влагой диоксида углерода и углеводородов.
· тонкая очистка газа до 0,1 – 0,5 мг/м;
· простота и надежность метода.
Недостатками процесса являются:
- загрязнение поверхности адсорбента за счет коксообразования;
- разрушение кристаллической решетки адсорбента под воздействием кислот - необходимость замены, а также большие потери давления в слое адсорбента.
Типичная установка адсорбционной осушки с высокотемпературной регенерацией адсорбента включает два адсорбера с неподвижным слоем адсорбента, каждый из которых проходит попеременно следующие стадии:
· адсорбция при температуре 35 - 50°С, давлении 8-12 МПа, длительности контакта газа с адсорбентом не менее 10 с (скорость газа в аппарате 0,15 - 0,30 м/с);
· нагрев адсорбента, который производится после переключения аппарата с режима адсорбции на десорбцию. Нагрев ведется горячим газом из трубчатого нагревателя со скоростью не более 60°С в час;
· десорбция - вытеснение из пор адсорбента поглощенной воды и восстановление его адсорбционной активности. Она начинает происходить, когда температура адсорбента достигнет 200-250 °С (для силикагелей) или 300 - 350 °С (для цеолитов). Горячий газ в периоды нагрева и десорбции проходит слой адсорбента в направлении, противоположном направлению осушаемого газа в периоде адсорбции (т. е. снизу вверх);
· охлаждение адсорбента, его начинают после завершения десорбции и переключения аппарата на режим адсорбции (осушки). Охлаждение ведут исходным холодным газом [8].
На настоящий момент адсорбционная осушка газа в Российской Федерации еще не получила широкого применения, по сравнению с абсорбционной осушкой. Главным критерием сдерживания внедрения процесса адсорбционной осушки природного газа является увеличение капиталоемких затрат на техническое перевооружение абсорбционных установок газа. Тем не менее адсорбционный процесс получил широкое распространение в Российской Федерации и ряде других зарубежных стран для осушки сжиженного природного газа для промышленного применения.
Газ при низкотепературной сепарации очищается за счет низких температур, причем при его охлаждении одновременно выделяется жидкий углеводород и влага, от которых избавляются с помощью сепараторов.
В зависимости от способа получения низких температур, сепараторы могут быть: с дросселированием газа высокого давления (изоэнтальпийный процесс), с искусственным холодом, с турбодетандерным агрегатом (изоэнтропийный процесс) и вихревой трубой. Чтобы предотвратить образование гидратов перед теплообменниками в газ добавляют метанол или гликоли.
Осушка газа при низкотемпературной сепарации имеет ряд достоинств:
· извлечение жидких углеводородов одновременно с осушкой газа; простота в эксплуатации и техническом обслуживании;
· простота автоматизации процесса в условиях промыслов;
· возможность постепенного дополнения и развития технологической схемы холодильниками и компрессорными машинами при снижении пластового давления.
Как следствие результативность понижения потока при изоэнтальпийном расширении газа с рекуперацией холода при 10–12 °С на 1 МПа перепада давления. Схема подготовки природного газа и газоконденсата представлена на рис. 4. Газ из скважины по шлейфу поступает в блок входного сепаратора, где происходит отделение капельной влаги, механических примесей, улавливание жидкостных пробок (в случае залпового выброса) от газа. Далее перед теплообменником вводится ингибитор гидратообразования с целью снижения рисков закупоривания проходного сечения технологических трубопроводов при образовании гидратов в процессе охлаждения. Проходя через дроссель/детандер/вихревую трубу, происходит охлаждение газа и выпадение капельной жидкости. Выделившаяся из газа при снижении температуры жидкость (вода, диэтиленгликоль, конденсат) отделяется от газа в сепараторе, откуда поступает в конденсатосборник [9].
Когда запаса пластовой энергии будет недостаточно для получения необходимой температуры сепарации за счет дросселирования газа, должны быть применены холодильные машины (установка холодильных машин).
Очищенный и осушенный газ из сепаратора поступает в межтрубное пространство теплообменника и далее в газосборный коллектор.
У данного метода осушки газа есть ряд преимуществ:
· Технология низкотемпературной сепарации пригодна для любой климатической зоны, допускает наличие в газе неуглеводородных компонентов, обеспечивает степень извлечения конденсата до 97 %, a также температуру точки росы, при которой исключается выпадение влаги и тяжёлых углеводородов при транспортировании природного газа;
· низкие капитальные и эксплуатационные затраты (при наличии свободного перепада давления).
Среди недостатков выделяют:
· низкие степени извлечения конденсатообразующих компонентов из тощих газов;
· непрерывное снижение эффективности в процессе эксплуатации за счёт облегчения состава пластовой смеси;
· необходимость коренной реконструкции в период исчерпания дроссель-эффекта.
На рис. 5 представлен 3S-сепаратор для инициирования ускорения закрученной среды природного газа до скорости выше звуковой, образования конденсата, разделения целевых фракций газа и торможения потока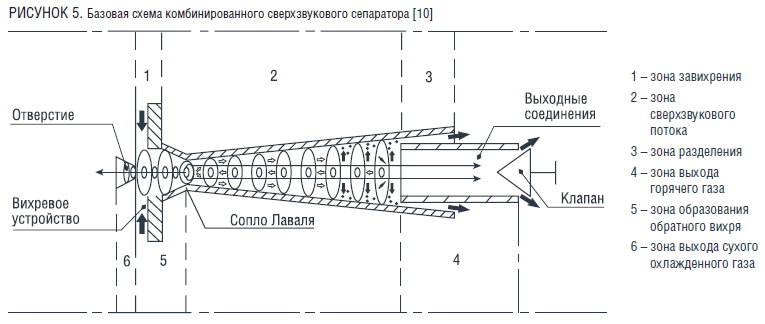
В 3S-сепараторе преобразование осевой скорости в тангенциальную происходит в дозвуковом режиме, поэтому после рабочей области аппарата не возникает косой ударной волны. В то же время газ расширяется до сверхзвуковой скорости в закрученном состоянии в расходящемся сечении сопла Лаваля. Одновременное возникновение завихрения и конденсации может эффективно уменьшить негативные последствия повторного испарения капель и повысить эффективность разделения сепаратора. Закручивание потока газа выше скорости звука происходит в интервале от –50 до –100 °С, что ведет к глубокому извлечению заданных целевых углеводородов из природного газа в 3S-сепараторе. Слияние НТС с 3S-технологией применимо для получения фракции С5+, воды, а также углеводородов С2+ (рис. 6).
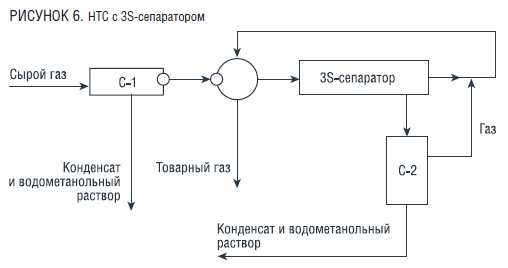
Устройство 3S-сепаратора с НТС состоит из блока охлаждения газа в сепараторе С-2, в который попадает частично поступивший газ – двухфазный поток из 3S-сепаратора. На основании этого при сверхзвуковом охлаждении газа в сверхзвуковом сепараторе происходит разделение на двухфазный поток, в первом потоке находятся образовавшиеся компоненты углеводородов, а во втором потоке – очищенный от углеводородов газ. Применение схемы НТС со сверхзвуковым сепаратором конструктивно уменьшает размеры установки и влияет на металлоемкость всего оборудования при проектировании, что значительно сокращает эксплуатационные и обслуживающие затраты. Отсутствие в сверхзвуковом сепараторе подвижных частей способствует высокой надежности [12].
Сверхзвуковой сепаратор исключает гидратообразование и процесс регенерации по причине короткого времени пребывания газа в устройстве, что удешевляет процесс подготовки природного газа и повышает экологическую безопасность производства. Однако сверхзвуковые сепараторы на сегодняшний день минимально представлены в полевых условиях, несмотря на многочисленные преимущества по сравнению с другими методами обезвоживания газа. В основном это объясняется неизученным в полной мере конструктивом и рабочих параметров, которые следует контролировать для обеспечения оптимального обезвоживания устройства для сверхзвуковой сепарации [13].
На сегодняшний день разработано большое количество сепараторов, с различной конструкцией, местом расположения в технологической схеме и сепарирующей силе. Основным классификационным признаком разделения сепараторов на различные виды является природа сепарирующей силы, по которой они подразделяются на гравитационные и инерционные. Гравитационные сепараторы основаны на разделении потока веществ под действием силы тяжести. Конструктивно это сосуды большего чем трубопровод диаметра, в которых скорость восходящего или горизонтального потока газа настолько мала, что твердые и/или жидкие частицы успевают осесть на дно, откуда периодически удаляются. А в инерционных сепараторах поток веществ разделяется под действием инерционных сил, приводящих к осаждению твердых и/или жидких частиц. Конструктивно они бывают насадочными (инерционная сила возникает в насадочных элементах, образующих извилистые каналы движения потока газа) и центробежными (инерционная сила возникает в центробежных элементах, преобразующих поступательное движение потока газа в центробежное).
Для сухой очистки применяют циклоны, принцип действия которых основан на центробежной силе. Для мокрой газоочистки используют скрубберы, пенные аппараты. Достоинством этих устройств является простота конструкции. Эти устройства пригодны, главным образом, для предварительной, грубой очистки.
Очистка от кислых газов, сернистых соединений, инертных газов, затрудняющих процессы переработки, проводится с помощью:
- абсорбции, основанной либо на химическом связывании кислых газов и сернистых соединений;
– хемосорбции, либо на растворимости кислых компонентов;
– физической абсорбции, а также их комбинирования.
Для физической абсорбции в качестве растворителя используют метанол или воду. Последний используется чаще, в связи с доступностью и дешевизной абсорбента, но имеет ряд таких недостатков, например, как низкая поглотительная способность по диоксиду углерода и невысокая селективность. Для удаления кислых газов могут использоваться метилпирролидон, гликоли (ди-, три-, этиленгликоли), трибутилфосфат, сульфолан, метанол и другие.
Когда в составе газа значительное количество Н2S и СО2 очистку проводят с помощью ДЭГ и ТЭГ, что упрощает технологию очистки, так как вместе с кислыми компонентами абсорбируется и водяной пар.
При хемосорбции взаимодействие кислых газов с активными компонентами абсорбента, приводит к образованию химических соединений, легко распадающихся на исходные компоненты при повышении температуры. В качестве связывающего агента для удаления Н2S применяют алканоамины (моно-, ди- и триэтаноламины, диизопропаноламины), щелочи. Для удаления СО2 в этот ряд включают и растворы карбонатов [11].
Недостатки процесса выражаются в:
- больших энергозатратах (около 70 %) на регенерацию абсорбента и получении тепла;
- коррозионной активности алканоаминов.
Решением вопроса является добавление в раствор этаноламинов ингибиторов коррозии в пределах защитной концентрации, что позволяет уменьшить циркуляцию абсорбента, то есть сократить энергозатраты на перекачку, повысить производительность установки, снизить скорость коррозии оборудования.
- адсорбции, основанной на поглощении кислых компонентов твердыми поглотителями. Адсорбцию применяют, когда необходимо снизить содержание до нормативного уровня. Адсорбционные процессы очистки так же делятся на химические - необратимая адсорбция без регенерации адсорбента, и физические - обратимая адсорбция на поверхности абсорбента.
Физическая адсорбция может протекать на активных углях, на силикагелях и алюмогеле. Но малая емкость из-за соадсорбции тяжелых углеводородов делает их неперспективными и, в основном, в промышленности для очистки применяются синтетические цеолиты, обладающие избирательностью к полярным молекулам и высокой абсорбционной емкостью. СО2 и Н2S успешно поглощаются молекулярными ситами марки СаА, NaХ и NaА. Стадия десорбции проводится нагреванием адсорбента, вакуумированием, продувкой инертным газом и требует значительных энергозатрат. Промышленное применение среди химических методов нашли окислы железа и цинка. Но данные процессы получили меньшее распространение в связи с невысокой технологичностью, нерегенерируемостью и необходимостью утилизации отработанного сорбента.
Кроме указанных методов очистки газов от кислых компонентов существуют еще каталитические методы, основанные на окислении и восстановлении кислых газов в присутствии катализаторов из никеля, кобальта и других. В промышленности нашли применение окислительные методы, заключающиеся в окислении сероводорода до элементарной серы или меркаптанов – до дисульфидов.
Достоинством процесса является селективность, при отсутствии необходимости извлечения СО2. Недостатком - протекание побочных реакций, что приводит к повышенному расходу реагентов, отложениям на стенках оборудования и коррозии. Восстановительные реакции протекают при взаимодействии оксидов серы с водородом (гидрирование) или водяным паром (гидролиз), а также при гидрировании диоксида углерода до метана. В настоящее время одно из перспективных направлений для очистки и осушки газа - применение мембранных технологии.
На примере подготовке газа перед сжижением (крупнотоннажным и малотоннажным) рассмотрим последовательность основных технологических процессов, а также выбор методов подготовки.
Установка очистки от кислых газов (УУКГ). В качестве требования рассмотрим очистку сырьевого газа от CO2 до объемного содержания менее 50 млн-1 и от H2S до объемного содержания менее 3,5 млн-1.
Рассмотрим различные варианты установки очистки.
Вариант 1: УУКГ на основе традиционной технологии аминовой очистки;
Вариант 2: Удаление CO2/H2S с использованием мембранной технологии;
Вариант 3: Использование молекулярных сит (адсорбция с колебаниями температуры);
Вариант 4: Процесс адсорбции с колебаниями давления или короткоцикловой адсорбции (КЦА);
Вариант 5: Низкотемпературная сепарация.
Рассмотрим отклоненные варианты: вариант 2 отклонен по следующим причинам:
· Отсутствие опыта применения на заводах СПГ на сегодняшний день;
· Неподтвержденная способность достижения требуемых уровней содержания CO2 (при использовании мембранных установок зафиксировано достижение уровня CO2 ~2%);
Вариант 3 отклонен по следующим причинам:
Хотя данная технология подходит по жестким требованиям к содержанию CO2, она требует большого расхода газа регенерации.
Вариант 4 отклонен, поскольку он ранее не применялся на заводах по производству СПГ. По расчетам, установка КЦА будет нуждаться в большом количестве слоев и адсорбента.
Вариант 5 был отклонен, поскольку он увеличивает сложность проекта, не имея подтвержденного опыта промышленного применения в масштабах.
Исходя из вышеизложенного, выбор был остановлен на УУКГ с использованием аминового растворителя (Вариант 1). Это традиционное решение, которое применяется практически на всех заводах по производству СПГ:
Использование растворителей ADIP-X/Sulfinol-X, обеспечивающих высокую эффективность абсорбции, что позволяет уменьшить размеры оборудования (в частности, аминового абсорбера и регенератора).
Установка осушки необходима для того, чтобы обеспечить объемное содержание воды в сырьевом газе менее 1,0 млн-1, что является стандартным требованием, обычно применяемым на проектах СПГ. Рассмотрим показанные ранее методы:
ТЭГ/МЭГ - как правило, при использовании данной технологии достигается объемное содержание воды в газе до 150 млн-1, что в значительной степени обусловлено равновесием в системе "вода-газ-МЭГ/ТЭГ". Поскольку это значение намного выше целевого уровня содержания воды в газе, данная технология не подходит для применения при производстве СПГ.
Теоретически, достижение требуемых характеристик может обеспечить охлаждение газа (метод низкотемпературной сепарации). Чем больше охлаждается поток газа, тем большее количество воды может конденсироваться из потока, и тем ниже будет содержание воды в газе. Для соответствия установленным требованиям необходимо применение ингибиторов с целью предотвращения образования гидратов под воздействием низких температур - наряду с обеспечением надлежащего отделения конденсированных капель воды, увлекаемых с потоком газа, это означает, что в действительности достижение целевого показателя будет затруднительным. Технические затруднения, связанные с достижением требуемого показателя эффективности, а также уровень мощности компрессоров, необходимый для повторного компримирования газового потока после охлаждения делают данный вариант технологии неприемлемым для применения на производстве СПГ.
Последним рассмотренным вариантом технологии является применение твердых влагопоглотителей. Эта технология хорошо зарекомендовала себя при глубокой осушке потоке газа. Использование силикагелей и активированной окиси алюминия способно обеспечить содержание влаги на уровне 10 и 5 млн-1, а молекулярных сит - до 0,1 млн-1. Для обеспечения требуемых показателей по содержанию воды в газе для производства СПГ единственным приемлемым решением представляется технология молекулярного сита.
С учетом рассмотренных методов подготовки технологическая схему будет выглядеть следующим образом (рис.8).
Заключение
В рамках данной работы была проведена оценка методов подготовки природного газа: абсорбции, адсорбции и сепарации, необходимых для выполнения требований нормативной документации по составу транспортируемого газа по магистральным газопроводам. У всех рассматриваемых методов проведен комплексный анализ протекающих технологических процессов, состава оборудования и выделены основные преимущества и недостатки данных решений, позволяющих осуществить выбор той или иной технологии в зависимости от исходных данных.
По результатам анализа по выбранным критериям методом экспертной оценки произведен выбор основных технологических решений при подготовке сжиженного природного газа при крупнотоннажном производстве.
Литература
1. Васильев, Г. Г. Обустройство промыслов: Учебное пособие / Г. Г. Васильев, А. П. Сальников. – Москва: Российский государственный университет нефти и газа (национальный исследовательский университет) имени И.М. Губкина, 2018. – 116 с.
2. Комплексный подход к цифровизации освоения арктических месторождений / С. М. Ватузов, К. С. Резанов, И. М. Ванчугов [и др.] // Деловой журнал Neftegaz.RU. – 2022. – № 9(129). – С. 70-81.
3. Ванчугов, И.М. Получение СПГ как метода утилизации ПНГ / И. М. Ванчугов, С. М. Ватузов, К. С. Резанов [и др.] // Деловой журнал Neftegaz.RU. – 2023. – № 1(133). – С. 71-75.
4. ГОСТ 5542-2014 «Газы горючие природные промышленного и коммунально-бытового назначения. Технические условия»
5. Лутошкин Г.С. Сбор и подготовка нефти, газа и воды к транспорту.—М.: Недра, 1972.—324 с
6. Кобилов, Х. Х. Низкотемпературная сепарация углеводородов из природного и нефтяного попутных газов / Х. Х. Кобилов, Д. Ф. Гойибова, А. П. Назарова. — Текст: непосредственный // Молодой ученый. — 2015. — № 7 (87). — С. 153-155. — URL: https://moluch.ru/archive/87/14912/ (дата обращения: 04.04.2023).
7. Билянский, К. В. Подготовка газа методом абсорбции / К. В. Билянский, О. М. Дарбазанов // Молодой ученый. – 2018. – № 50(236). – С. 41-43.
8. Шевкунов, С. Н. Адсорбционная осушка и низкотемпературная ректификация в процессах промысловой подготовки природного газа / С. Н. Шевкунов // Экспозиция Нефть Газ. – 2016. – № 7(53). – С. 46-49.
9. Яркеева, Н. Р. К вопросу об эффективности технологии низкотемпературной сепарации / Н. Р. Яркеева, И. А. Ишбулатов // . – 2019. – Т. 17, № 1. – С. 13-23. – DOI 10.17122/ngdelo-2019-1-13-23.
10. Китов, Е. С. Анализ технологий промысловой подготовки природного газа / Е. С. Китов, В. И. Ерофеев, С. Н. Джалилова // Известия Томского политехнического университета. Инжиниринг георесурсов. – 2022. – Т. 333, № 10. – С. 31-38. – DOI 10.18799/24131830/2022/10/3885.
11. Муллахметова, Л. И. Попутный нефтяной газ: Подготовка, транспортировка и переработка / Л. И. Муллахметова, Е. И. Черкасова // . – 2015. – Т. 18, № 19. – С. 83-90.
12. Carroll J. Natural gas hydrates: a guide for engineer. Burlington, Gulf Professional Publ., 2020. 400 p
13. Vlasenko, V. S. Combined supersonic separator for FPSO / V. S. Vlasenko, V. V. Slesarenko, G. M. Karpov // Proceedings of the International Offshore and Polar Engineering Conference – Sapporo, 2018. – P. 1289-1294