Технический углерод представляет из себя полидисперсные мелкие частицы углерода, образующиеся при неполном сгорании углеводородного сырья. Технический углерод является крупнотоннажным нефтехимическим продуктом, его мировое производство составляет более 13 млн тонн/год [1].
Основной областью применения технического углерода является производство резинотехнических изделий. К прочим областям применения можно отнести производство пластмасс, лакокрасочных материалов, бумаги и различных покрытий. Использование технического углерода в качестве наполнителя в реакциях вулканизации каучука позволяет на порядок увеличить прочность резинотехнических изделий.
В виду высоких затрат на транспортировку технического углерода из-за низкого объемного веса целесообразно размещать заводы-производители в непосредственной близости к заводам-потребителям.
На крупных российских предприятиях применяются две основные технологии производства технического углерода, которые отличаются друг от друга типом сырья, способом разложения углеводородов и организацией процесса.
На сегодняшний день основным методом производства технического углерода в России является печной. Данный процесс проходит в непрерывном турбулентном пламени в реакторах проточного типа при температуре 1000–1500 °С. Жидкие углеводороды форсунками впрыскиваются в поток газов полного сгорания топлива и разлагаются в результате термоокислительного воздействия. Реакционную смесь подвергают охлаждению впрыском воды, а технический углерод улавливают в циклонах, на рукавных фильтрах или электрофильтрах.
Принципиальная технологическая схема производства технического углерода печным методом представлена на рисунке 2.
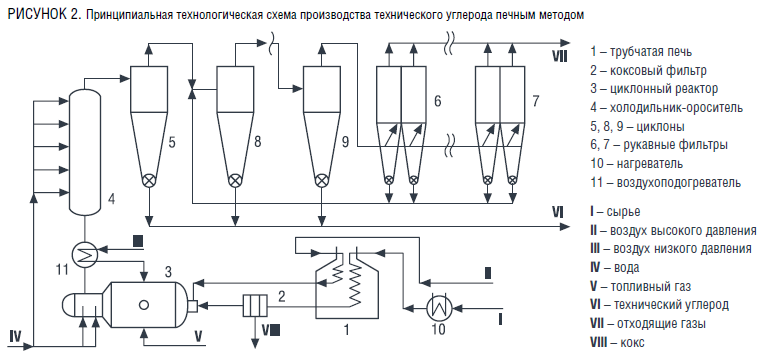
Сырье через подогреватель 10 проходит в трубчатую печь 1, где нагревается до 350–500 °С. Образующийся при нагревании кокс отделяется на коксовом фильтре 2. Воздух высокого давления и сырье смешиваются и подаются в циклонный реактор 3, где в течение 0,02–0,04 с при температуре 1250–1500 °С происходит термоокислительное разложение сырья. Для снижения доли сгорающего сырья в реактор 3 также подается топливный газ и воздух низкого давления через воздухоподогреватель 11. Реакционная смесь охлаждается водой на выходе из реактора и в холодильнике-оросителе 4, технический углерод отделяется сначала в циклонах 5, 8 и 9, а затем на рукавных фильтрах 6 и 7, после чего направляется на грануляцию. Отходящие газы проходят ступени очистки и утилизации.
Термический процесс получения технического углерода основан на разложении природного газа в нескольких переменно работающих реакторах. В один из реакторов подают воздух в смеси с природным газом, где за счет его горения разогревается поверхность футеровки, а во второй предварительно разогретый реактор подается природный газ, который при термическом разложении образует технический углерод.
Принципиальная технологическая схема производства технического углерода термическим методом представлена на рисунке 3.
Процесс проходит в печных реакторах 1 и состоит из двух циклов по 5–8 минут каждый: во время цикла нагрева газ сгорает и разогревает огнеупорную футеровку, представляющую собой решетчатую систему из огнеупорных кирпичей для увеличения поверхности нагрева, до температуры около 1600 °С, при достижении которой подача воздуха в реактор перекрывается, а продукты сгорания удаляются, во время цикла разложения в реактор вводится сырье и водород, в ходе эндотермической реакции футеровка реактора остывает до температуры около 1200 °С и потоки переключаются. Реакционная смесь охлаждается в холодильнике-оросителе 2, полученную сажу отделяют в циклоне 3 и электрофильтре 4, после чего отходящие газы направляются на очистку и утилизацию, а технический углерод – на грануляцию [2].
Также для получения особо чистого технического углерода применяется термическое разложение ацетилена, которое является экзотермической реакцией, вследствие этого ацетиленовый метод не требует подвода тепла и после инициации процесс проходит непрерывно [3].
На сегодняшний день основными крупнотоннажными предприятиями, осуществляющими производство ТУ являются:
- АО «ЯТУ имени В.Ю. Орлова»,
- ООО «Омсктехуглерод»,
- АО «Нижнекамсктехуглерод»,
- ОАО «Волгоградский завод технического углерода»,
- ОАО «Туймазытехуглерод»,
- Сосногорский газоперерабатывающий завод (рисунок 4).
«Ярославский технический углерод имени В.Ю. Орлова»
Предприятие АО «ЯТУ имени В.Ю. Орлова» выпускает 23 марки технического углерода «N» и «П» мощностью более 310 тыс. тонн/год.
В качестве сырья для производства технического углерода применяются антраценовое масло, тяжелый газойль каталитического крекинга, мазут, тяжелая смола пиролиза, поставляемые ПАО «Славнефть-ЯНОС», смешиваемые в определенных соотношениях.
Предприятие реализует печной способ производства с разложением сырья в присутствии кислорода воздуха в реакторе при температуре 1400–1800 °С. Улавливание образовавшегося технического углерода проходит при помощи рукавных фильтров. Грануляцию продукта осуществляют мокрым методом с последующей сушкой в сушильных барабанах.
С 2010 года мощность предприятия по выпуску технического углерода возросла с 220,8 тыс. тонн до 312,6 тыс. тонн в 2022 году (рисунок 5) [4].
«Омсктехуглерод»
ООО «Омсктехуглерод» – одно из крупнейших предприятий по производству технического углерода мощностью более 280 тыс. тонн технического углерода в год, ассортимент продукции представлен более чем 30 марками технического углерода «N» и «П» для производства резинотехнических изделий. С 2010 года предприятие также выпускает марки специального назначения «OMCARB» для производства лакокрасочных материалов, пластиков и пигментов.
В качестве сырья для производства технического углерода применяются тяжелая смола пиролиза, тяжелый газойль каталитического крекинга, поставляемые АО «Газпромнефть-ОНПЗ», и коксохимическое сырье.
Получение технического углерода осуществляется в прямоточных цилиндрических реакторах за счет разложения смеси нефтяного и коксохимического сырья в потоке дымовых газов. Для прекращения реакции разложения в поток углеродно-газовой смеси выпрыскивается вода. Улавливание образовавшегося технического углерода проходит при помощи рукавных фильтров с последующим гранулированием и сушкой.
С 2010 года мощность предприятия по выпуску технического углерода возросла со 172,8 тыс. тонн/год до 197,7 тыс. тонн в 2022 году (рисунок 6).
«Нижнекамсктехуглерод»
АО «Нижнекамсктехуглерод» – нефтехимический актив ПАО «Татнефть» производительностью более 135 тыс. тонн технического углерода в год.
Ассортимент продукции представлен 14 марками технического углерода «N» и «П».
В качестве сырья для производства технического углерода применяются тяжелая смола пиролиза, тяжелый газойль каталитического крекинга, поставляемые АО «ТАНЕКО» и АО «ТАИФ», и коксохимическое сырье.
Технический углерод на АО «Нижнекамсктехуглерод» получают печным способом.
Получение технического углерода осуществляется печным способом в цилиндрическом реакторе при температуре 1300–1800 ℃. Для прекращения реакции и сохранения необходимых свойств технического углерода производится охлаждение аэрозоля путем впрыска технологической воды.
Образовавшаяся углеродно-газовая смесь поступает в блок улавливания для выделения технического углерода при помощи циклона-концентратора и рукавного фильтра. Выделенный технический углерод поступает в блок обработки, где происходит процесс уплотнения технического углерода в смесителе–грануляторе мокрым способом. Мокрые гранулы технического углерода поступают в сушильный барабан и далее на узел распределения готовой продукции.
С 2010 года мощность предприятия по выпуску технического углерода возросла со 117,5 тыс. тонн до 135,6 тыс. тонн в 2022 году (рисунок 7).
«Волгоградский филиал Омсктехуглерод»
ОАО «Волгоградский завод технического углерода» с 2005 года входит в состав ООО «Омсктехуглерод» и производит те же марки технического углерода резинотехнического и специального назначения мощностью более 169 тыс. тонн в год из аналогичного сырья и по схожим технологиям.
С 2010 года мощность предприятия по выпуску технического углерода возросла со 101,3 тыс. тонн/год до 169,2 тыс. тонн в 2022 году (рисунок 8).
ОАО «Туймазытехуглерод» производит технический углерод марок «П» и «Т» мощностью более 31 тыс. тонн/год.
В качестве сырья для производства технического углерода применяются антраценовое масло, мазут, каменноугольная смола, природный газ.
Получение печного технического углерода производится путем окислительного разложения сырья при температуре 1100–1300 °С, достигаемой сжиганием природного газа в топочной части реактора. Для прекращения реакции в реакционную смесь впрыскивается технологическая вода. Образовавшийся технический углерод осаждается на электрофильтрах.
Получение термического технического углерода производится в двух реакторах периодического действия при температуре более 1100 °С. Углеродно-газовая смесь охлаждается в водяном холодильнике. Технический углерод улавливается в циклонах и на рукавных фильтрах.
С 2010 года мощность предприятия по выпуску технического углерода возросла со 17,2 тыс. тонн до 31,3 тыс. тонн в 2022 году (рисунок 9).
Сосногорский газоперерабатывающий завод
Сосногорский газоперерабатывающий завод принадлежит компании ООО «Газпром переработка» и производит технический углерод марок «П» мощностью более 11 тыс. тонн/год и «Т» мощностью более 5 тыс. тонн/год.
В качестве сырья для производства технического углерода применяются сухой отбензиненный газ и газ стабилизации газового конденсата непосредственно с Сосногорского ГПЗ.
Получение печного технического углерода производится путем неполного сгорания сырья, вводимого в реактор при температуре 1180–1300 °С. Охлаждение углеродно-газовой смеси происходит путем впрыска технологической воды. Технический углерод улавливается на электрофильтрах.
Получение термического технического углерода производится в цилиндрических реакторах периодического действия при температуре 1200–1500 °С. Охлаждение углеродно-газовой смеси и улавливание технического углерода осуществляется в скруббере Вентури.
С 2010 года мощность предприятия по выпуску термического технического углерода снизилась с 31,6 тыс. тонн до 16,9 тыс. тонн в 2022 году (рисунок 10) [5].
В настоящее время большая часть технического углерода в России производится по печной технологии, имеющей высокую технологическую гибкость и не требующей высокой степени автоматизации. Термические марки технического углерода из газового сырья производят два предприятия: Туймазытехуглерод и Сосногорский ГПЗ. В связи с низким выходом целевого продукта и низкими показателями экологической безопасности с 2013 году технический углерод по канальной технологии в России не производится. Вследствие низкого спроса на ацетиленовую сажу (узкие области применения) и высокой стоимости сырья доля технического углерода, получаемого из ацетилена, в российском производстве невелика.
В связи с резким снижением экспорта технического углерода производительность некоторых предприятий в 2022 году была снижена. Рост внутреннего спроса на резинотехнические изделия обуславливает прирост производительности некоторых предприятий по производству стандартных марок технического углерода. Рост внутреннего спроса на лакокрасочные материалы обуславливает резкий рост производительности предприятий по производству специальных марок технического углерода (Омсктехуглерод и Волгоградский завод технического углерода).
Литература
1. Исследование влияния технического углерода на свойства изопреновых эластомеров/ Макаров И.С. [и др.] // Ползуновский вестник. – 2022. – № 1. – С. 154–163.
2. Гюльмисарян Т.Г., Левенберг И.П. Технический углерод в предстоящие годы // Макрохем. – 2018. – № 3. – С. 3–8.
3. Раздьяконова Г.И., Кохановская О.А. Состояние и перспективы развития производства технического углерода (обзор) // Каучук и резина. – 2013. – № 3. – С. 10–15.
4. Денисова Е.С., Зиновьева О.О. Оценка экологической безопасности предприятий по производству технического углерода //Динамика систем, механизмов и машин. – 2014. – № 4. – С. 208–211.
5. Голубева И.А., Родина Е.В. Сосногорский газоперерабатывающий завод (ООО «Газпром переработка») // Нефтепереработка и нефтехимия. Научно-технические достижения и передовой опыт. – 2015. – № 1. – С. 26–33.