Перед тем как подробно рассмотреть кейсы, связанные с виртуальным вводом в эксплуатацию и обучением персонала, нужно рассмотреть классический подход к процессу разработки систем автоматизации производства, проведению пусконаладочных работ и реализации сервисного обслуживания. Благодаря этому мы сможем определить основные преимущества новых сценариев, выделить точки оптимизации, которые помогут повысить эффективность разработки систем автоматизации производства и качественно улучшить результат подготовки специалистов-операторов систем автоматизации технологических процессов.
На схеме 1 представлен классический подход процесса разработки систем автоматизации «от концепции - до конечного результата», который включает в себя два этапа:
-
Первый – проектирование
-
Второй – производственный участок

Схема 1
Все это приводит к значительным временным потерям и существенно увеличивает переход на следующий этап (производственный участок), при этом имеет место дополнительные финансовые издержки и непредсказуемые сроки, так как зачастую точно определить, сколько времени уйдет на решение и дополнительную проверку всех элементов одной цепочки, крайне затруднительно.
Когда полностью завершен этап проектирования, осуществляется переход к следующему этапу – производственный участок. Сразу после проведения монтажных работ требуется провести пусконаладочные работы. На данном, особенно важном шаге, могут быть выявлены все недочеты и ошибки, которые не были локализованы ранее на предыдущем этапе. При возникновении подобных проблем, требуется проведение срочных правок выявленных ошибок, и, как правило все это приводит к тому, что промышленное оборудование находится в состоянии простоя дольше чем это планировалось, что так же приводит к значительным финансовым потерям. При этом, в случае внесения правок «на скорую руку» без проверки и валидации, существует вероятность возникновения авариных ситуаций, которые в свою очередь могут повлиять на весь технологический процесс в целом. Подобные случаи очень тяжело предсказать. Однако даже если все было выполнено качественно и оборудование введено в эксплуатацию без каких-либо трудностей, то в случае модернизации, требуется проходить этапы проектирования и производственного участка заново и пошагово. И зачастую, все проблемы, описанные ранее, могут подстерегать и в этом случае.
Особо стоит подчеркнуть обучение персонала работе с промышленным оборудованием, так как от этого процесса напрямую зависит работа оборудования.
При отсутствии цифрового двойника, полностью эмитирующего все процессы, которые проходят на промышленном объекте, качественного обучения персонала работе с оборудованием добиться крайне затруднительно. Тоже самое касается и подтверждения готовности правильно реагировать на внештатные ситуации, так как аварийной ситуации могут предшествовать неучтенные в инструкциях действия оператора.
Для предупреждения всех описанных выше проблем, компания Siemens предлагает воспользоваться решением для промышленности – виртуальный ввод в эксплуатацию. Данное решение позволит вывести всю инжиниринговую работу на качественно новый уровень. Благодаря использованию технологии цифровых двойников решение позволит значительно ускорить процесс ввода оборудования в эксплуатацию, проводить качественную подготовку специалистов-операторов и инженеров, проводить необходимые виртуальные тесты систем, машин, а также проводить виртуальную модернизацию с целью ее проверки перед внесением изменений в действующие системы, но самое главное что все это можно делать параллельно с работающей системой.
Если вспомнить предыдущую схему 1, то можно заметить строгую этапность процессов. Компания Siemens же предлагает в корне изменить структуру этапа проектирования и выполнять все элементы параллельно (см.схема 2).
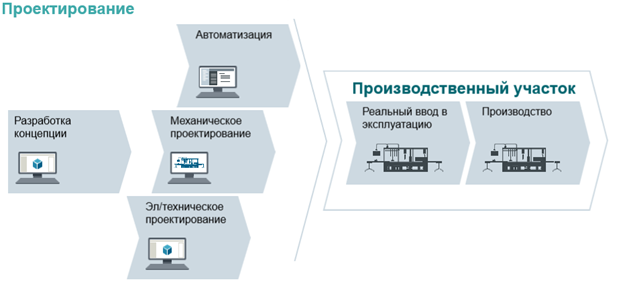
Схема 2
Теперь же, когда разработка систем автоматизации осуществляется параллельно с помощью инновационных продуктов от компании Siemens, становится возможным проведение любых исправлений, испытаний на любом из этапов без последствий. Так как при разработке возможно использовать «живой» цифровой двойник механики, систем автоматизации, непрерывных процессов, можно провести виртуальное тестирование, как и отдельного участка, так и всей системы в целом. Все локализованные ошибки могут быть сразу исправлены, а также проверен необходимый участок или же вся созданная система в виртуальном пространстве. Становится возможным тестировать различные аварийный сценарии автоматически, например, используя скрипты. При этом необязательно иметь полностью спроектированный объект, достаточно использовать концептуальные элементы. Например, для тестирования алгоритма управления приводной части, если требуется понять правильность созданной логики программируемого логического контроллера, необязательно создавать полный цифровой двойник приводного узла. Достаточно использовать виртуальный контроллер и функциональную схему разбора телеграмм в среде SIMIT, как например на схеме 3.

Схема 3
Siemens располагает широкой продуктовой линейкой инструментов виртуального ввода в эксплуатацию для любой индустрии, (см.схема 4).
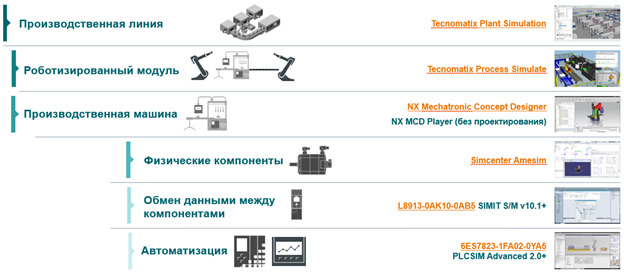
Схема 4
После разработки управляющей программы, для программируемого логического контроллера, в TIA Portal, с целью запуска и проверки созданной управляющей программы возможно использовать PLCSIM Advanced, данный софт поддерживает создание нескольких экземпляров симуляций обособленных контроллеров на одном компьютере, как и с внутренним подключением по софтверной шине, так и с выходом на сетевую карту для подключения панели реального/виртуального человеко-машинного интерфейса или же другого симуляционного или реального программируемого логического контроллера. Имеется поддержка разных сетевых протоколов, включая OPC UA, но самое главное – это полная эмуляция контроллера SIMATIC S7-1500, при этом программу под режим симуляции адаптировать не требуется, как она используется в реальном контроллере, так и может быть прогружена в виртуальный симуляционный контроллер. [1]
Для имитации обмена данными, например между контроллерами и частотными преобразователями можно воспользоваться частью функционала продукта SIMIT. Чтобы наладить обмен телеграммами между виртуальным Control Unit частотного преобразователя Sinamics и виртуальным контроллером Simatic S7 достаточно собрать блок разбора управляющей телеграммы и при этом, не внося никаких изменений, в управляющую программу программируемого логического контроллера, становится возможным предварительная наладка технологических объектов контроллера, а также их тестирование. Также SIMIT имеет достаточно богатый потенциал для построения цифрового двойника систем различных непрерывных технологических процессов, а это означает что становится возможно не только тестирование отдельных технологических элементов управляющей программы, но и всего процесса в целом, включая некоторые переходные процессы и т.д. Также доступен ввод необходимых сенсоров и датчиков, как аналоговых, так и дискретных со стороны цифрового двойника в виртуальный программируемый логический контроллер. [2].
Когда необходимо построить и рассчитать мультифизические системы, а также создать их цифровой двойник для последующих испытаний, то все это можно сделать с применением 1-D проектирования в системе Simcenter Amesim. Большой набор стандартных физических элементов позволяет собрать функциональную физическую схему и провести ее валидацию за считанные минуты. При этом данный продукт может быть легко соединен с другими системами симуляции. [3]
Для создания, расчета, проверки, проведения виртуальных испытаний механических элементов машин, обнаружения коллизий в процессе перемещения объектов, Siemens предлагает к использованию софтверный продукт NX Mechatronic Concept Designer, благодаря этому решению открывается возможность построения точных массогабаритных твердотельных моделей с физическими свойствами. Благодаря такому потенциалу валидация механизмов и их проверка значительно упрощается, так как все происходит в режиме 3D моделирования с возможностью полного погружения в виртуальную среду в режиме VR (Virtual reality). При этом для проведения тестирования, необязательно собирать точною копию механизмов, достаточно создать концептуальный цифровой двойник и наделить его необходимыми физическими свойствами. Доступен импорт твердотельных моделей из любых CAD систем, а для того что бы соединить цифровой двойник механического изделия с системой автоматизации, требуется всего лишь выбрать из списка доступных подключений необходимую систему симуляции, например SIMIT или PLCSIM Advanced, связать переменные и цифровой двойник уже готов работать с виртуальной системой АСУ ТП и включает в себя все те положительные опции, которые имеются в подсоединенных системах симуляции. При этом опускается использование виртуальных датчиков, как аналоговых, так и дискретных, скриптов тестирования и т.д. [4]
Когда речь заходит о роботизации, Siemens готов предложить решение Tecnomatix Process Simulate для проектирования и программирования систем роботизированных ячеек. Как и в предыдущем случае возможно не только создание необходимой инфраструктуры в разрезе роботизированных ячеек, но и валидации в режиме цифрового двойника с соединением с другими симуляционными средами, дополнительно данный продукт оснащен возможностью работать с режимом VR для полного погружения в роботизированную ячейку и позволяет проводить обучение робота непосредственно из VR. [5]
Подняться до уровня управления всем производственным процессом позволит софтверное решение от Siemens Tecnomatix Plant Simulation. Данный продукт отличается относительной неглубокой механической симуляцией, но в тоже время позволяет достаточно глубоко эмитировать логистические процессы любой сложности. Будь то это грузовой порт или небольшой складской участок. При этом данный инструментарий помогает заглянуть не только в симуляцию 1 к 1 и проверить сценарий «A что если?», но и благодаря ускорению времени, возможно узнать, что будет через несколько недель, лет, за относительно небольшой промежуток астрономического времени. Отдельный пункт посвящен помощи в оптимизации построения цепочек потока материала, а также расчету энергопотребления, как отдельных участков производства, так и всего объекта в целом. Идеальное сочетание уровня симуляции позволяет соединить SCADA систему для тестирования, при этом соединяясь с цифровым двойником промышленного объекта, SCADA система «будет думать» что работает с реальными элементами системы АСУ ТП. Также как и с предыдущими уровнями симуляции и разработки, возможно сочетание всех элементов для полной имитации любого технологического процесса. [6]
Подведя промежуточный итог, предложенный инструментарий позволят работать с цифровыми двойниками промышленных объектов любой сложности, соединя воедино все уровни систем, в одну общую цифровую экосистему. Для интеграции всех уровней симуляции компания Siemens предусмотрела возможности бесшовной интеграции продуктов через софтверную шину или другие протоколы передачи данных, например SMI или OPC UA. Благодаря решению виртуального ввода в эксплуатацию, становятся возможны любые проверки систем автоматизации, облегчается поиск и локализация ошибок, ускоряется процесс проектирования в целом. Так как основная часть пусконаладочных работ уже была проведена без реального оборудования в виртуальном пространстве, при условии качественно проведенных виртуальных испытаниях, становится возможно значительно сократить пусконаладочные работы, а ведь в конечном итоге это приведет к значительной экономии средств.
Тем более имея цифровой двойник, задачи по модернизации и оптимизации уже введенных объектов, с применением технологий виртуального ввода в эксплуатацию, могут быть так же выполнены в виртуальном пространстве с целью оптимизации процесса разработки и реальной пусконаладки, например появление внештатных ситуаций будет сведено к минимуму после переналадки производства, так как все необходимые тестирования системы уже были проведены в виртуальном пространстве и поведение системы при работе в новых режимах уже известно.
Что же касается обучения персонала использованию, обслуживанию машин, то именно благодаря созданию цифрового двойника при помощи комплекта виртуального ввода в эксплуатацию от Siemens возможно значительно улучшить качество этого процесса. Например, на рисунке 1 показан типовой сценарий обучения оператора технологической машины при помощи созданного цифрового двойника.

Рисунок 1
Главное преимущество обучения оператора при помощи технологии цифрового двойника – полная эмуляция всего технологического процесса любой сложности. Также если использовать полный функционал человеко-машинного интерфейса базе WinCC от Siemens, можно заготовить специальные подсказки с алгоритмами действий, инструкциями при различных аварийных сценариях для ускорения подготовки специалиста.
Что же касается технологии VR (Virtual Reality), то ее потенциал компания Siemens раскрывает не только для глубокого изучения конструкции промышленных машин и механизмов, но и для оценки эргономики рабочего места специалиста. Например, при использовании технологии Motion Capture, в среде Process Simulate имеется возможность использовать цифровой двойник человека для наиболее четкого представления эргономики рабочего пространства того или иного специалиста. Так же изучение конструкций в среде NX Mechatronic Concept Designer поддерживает работу в режиме коллаборации VR и позволяет полностью погрузить в виртуально пространство сразу нескольких человек для детального изучения конструкций устройств любой сложности, коллеги так же могут проводить виртуальную сборку или разборку устройств с целью получения необходимых знаний о конструкции, например рисунок 2.

Рисунок 2
Стоит также отметить, что это всего лишь один из многих цифровых инструментов от компании Siemens, который является частью одной цифровой экосистемы Digital Enterprise
Литература:
-
Function Manual PLCSIM Advanced [Электронный ресурс] : Siemens industry online support URL: https://support.industry.siemens.com/ (дата обращения: 06.06.2020).
-
Manual SIMIT [Электронный ресурс] : Siemens industry online support URL: https://support.industry.siemens.com/ (дата обращения: 06.06.2020).
-
Description Simcenter Amesim [Электронный ресурс] : URL: https://www.plm.automation.siemens.com/ (дата обращения: 06.06.2020).
-
Description NX MCD [Электронный ресурс] : URL: https://www.plm.automation.siemens.com/ (дата обращения: 06.06.2020).
-
Description Tecnomatix Process Simulate [Электронный ресурс] : URL: https://www.plm.automation.siemens.com/ (дата обращения: 06.06.2020).
-
Description Tecnomatix Plant Simulation [Электронный ресурс] : URL: https://www.plm.automation.siemens.com/ (дата обращения: 06.06.2020).
Keywords: VR, virtual reality, virtual commissioning, digital twin, factory automation, process automation, operator training, simulation, SIMIT, NX MCD, Process Simulate, Plant Simulation, Totally Integrated Automation, TIA, SIMATIC S7, SINAMICS, WinCC, SCADA, HMI, PLCSIM Advanced, virtual controller, Motion Capture